
Situated in bustling central Birmingham and covering 34Ha of former industrial heartland, the Washwood Heath site will house the main depot and control centre for High Speed Two (HS2) – bringing 550 new jobs to the community.
​
But, as the largest brownfield site on the HS2 project, and with 1,450,000m3 of cut/fill to be value-engineered, plans for Washwood Heath could not become reality without a robust remediation strategy in place.
​
When it came to remediation of soils, one question held particular importance: how could we prevent an estimated 135,000m3 of material from leaving site with up to 60,000m3 potentially ending up in landfill or being incinerated, using cost-effective remediation methods befitting of a public project?
​
And how could we do it while ensuring efficient delivery on a time-critical infrastructure scheme, with multiple stakeholders to consider?
​
This entry will show how Jackson Remediation:
​
-
Used its expertise to reduce the volume of soils requiring treatment by 60%
-
Prevented 55,000m3 of soil from going to landfill (or incineration),
-
Preventing 35,886 wagon movements from clogging up Birmingham’s already congested roads
-
Saved BBV approx. £5M by avoiding hefty offsite disposal costs
-
Reduced programme time by approx. 12 weeks through efficient methods of remediation
-
Ensured strict compliance with the CL:AIRE DoW CoP and SuRF, providing detailed information for final verification
-
Provided invaluable support to stakeholders, including our immediate client, Duo Group, and ultimate client, Balfour Beatty Vinci (BBV)
​
​
​
​
​
​
​
​
​
​
From boom to bust, and back again
Washwood Heath has a rich industrial history, stretching back to the early 1900s.
​
Over the decades, the site held many uses, providing work for hundreds of local people. These included:
​
-
The pride of British automotive manufacturing was situated at the site, being the home of the Wolseley Motor Car Company and latterly Leyland DAF Vans (LDV) manufacturing facility. The site includes an area of historic landfilling adjacent to the River Tame (adjacent to the aptly named ‘Wolseley Drive’).
-
The former UK Mail depot. An area of approximately 6Ha that, until mid-2018, comprised a regionally critical distribution warehouse.
-
The former Alstom Works. An area of approximately 21Ha constructed on a platform 5m higher than the remainder of the site, until mid-2019, 19th century brick built rolling stock sheds that had accounted for around 50% of the total site area.
-
The CEMEX and Hanson plant. This comprised a ready-mix concrete plant, asphalt manufacturing plant and
-
hardstanding, covering approx. 6.5Ha.
​
But in 2009, a century of manufacturing ceased, and a once significant site fell silent. Left behind was wide-ranging soil
and groundwater contamination. Once this contamination was successfully managed, HS2 could bring the site back to regional significance, providing 550 new jobs and putting Washwood Heath back on the map.
​
​
​
​
​
​
​
​
​
​
​
​
​
A robust and sustainable solution
​
Jackson Remediation was appointed by Duo Group as technical remediation lead on the project.
Historic site investigations had identified a cocktail of differing contaminants, with receptors at significant risk from the contaminated soils and water at site, including the River Tame and the River Rea, which are both closely associated with the site.
​
The scale of the site required contaminated soils requiring affirmative remedial action to be characterised into three ‘types’ of soils:
​
Type-1 Soils (approx. 47,579m3):
​
Generally ashy Made Ground with Total Petroleum Hydrocarbon (TPH) impacts.
​
Type-2 Soils (approx. 28,000m3):
​
Broad range hydrocarbon fractions with an aliphatic/aromatic split in the region of 70:30, represented as hydrocarbon hotspots within the upper 1.5m of the soil profile.
​
Type-3 Soils (approx. 60,000m3):
​
These comprised a mixture of ash and slag gravel. Some of the highest concentrations of aromatic hydrocarbons (>58,000mg/kg) and Polyaromatic Hydrocarbon (>10,000mg/kg) were observed across the full vertical profile of highly variable Made Ground.
​
Treatment methods for both Type-1 and Type-2 soils had already been agreed. They would be taken for offsite treatment at a local hub then returned to site.
​
It was Type-3, more complex aromatic hydrocarbon impacted soils where the treatment solution remained undefined, and offsite disposal to landfill (or even incineration in the EU) appeared a real possibility.
​
Further options proffered for Type-3 included Stabilisation and Thermal Desorption. But were better value, more efficient solutions possible for all soils?
​
​
​
​
​
​
​
​
​
​
​
​
​
​
​
​
The Saltley Railway Carriage and Wagon Works, Washwood Heath, 1928
​
Additional investigations
​
Jackson Remediation deployed its Mobile Treatment Permit to control various activities on site (water treatment, screening and processing of hazardous soils) and included a range of potential on-site treatment solutions for Type 1, 2 and 3 soils.
The team proposed several trials based on a review of the historic data, initially looking at Type-1 & 2 soils and, subsequently, Type-3 soils.
​
“The on-site treatment of these heavily impacted soils has offered significant logistical benefits to our delivery of this high profile remediation and enabling earthworks project.”
​
Adam O’Reilly, HS2 Director, Duo Operations
​
​
​
​
​
​
​
​
​
​
​
​
​
​
​
​
​
​
​
​
​
​
​
​​
Planned Progress Monitoring
​
For the lesser impacted Type 1 & 2 soils, a range of bioremediation methods were trialled with the following determinants tested at the start of the trials and weekly (or daily) throughout:
​
-
Site Specific Assessment Criteria (SSAC) (mg/kg)
-
Moisture Content (%)
-
Nutrient Ratio (C:N:P)
-
pH
-
Particle Size Distribution
-
Temperature (in-situ probe)
-
Ground gasses (i.e. O2, CO2, CH4)
​
Upon completion of the trials a ‘bioaugmentation’ microbial additive was selected alongside a nutrient addition as a suitable treatment for Type 1 & 2 soils.
​
Type 3 soils were assessed to be impacted with such high concentrations and long-chain aromatics that bioremediation may have been significantly inhibited. Alongside enhanced bioremediation (using the same bioaugmentation inoculation), chemical oxidation methods were trialled and found to be successful. The success of on-site chemox allowed the potential for Type 3 soils to also be treated on-site avoiding off-site removal and landfill or incineration.
​
​
​
​
​
​
​
​
​
​
​
​
​
​
​
Artists impression: Aerial View of Washwood, Heath Depot
​
The works were conducted in accordance with the safe systems of work approved by Duo and BBV, including handling of potentially corrosive materials (chemox). Toolbox talks and frequent safety and compliance inspections were completed by all stakeholders.
“The work done by Jackson Remediation and Duo to maximise resource efficiency not only aligns with the HS2 sustainability goals, but has also been exemplary in terms of stakeholder engagement between HS2, the main contractor BBV and the Environment Agency.”
Steve Box, Lead Contaminated Land Engineer, WS2
​
Further Refinement
​
Once the preferred treatment designs were identified and instructed by the client, ‘failing materials’ were transported to the designated treatment area and ‘t=0’ samples were obtained. It was noted that some soils sentenced for treatment were not exceeding the SSACs based on t=0 samples. Consequently the excavation methodology and watching brief methods were reviewed resulting in JR being instructed to undertake a specific watching brief activities at the excavation face. The Remediation Implementation Plan was revised to alter the material sentencing protocols.
​
A new way forward: Bioremediation and Chemox
​
The revision to both the excavation methodology and treatment methods (namely on-site) received Environment Agency and HS2 approval and reduced the volume of Type 3 soils requiring treatment by approximately 60% and allowed in excess of 90% of all soils planned for off-site treatment (or disposal) to be retained on site. This critical change to the planned methods offered significant savings in terms of cost, programme, vehicle movement and CO2 reduction benefits.
​
Validation and Verification
​
All treated soils were meticulously tested and a ‘clearance report' issued for every treated stockpile. These reports were submitted to the BBV materials manager for approval and subsequent inclusion in the MMP verification report.
Impact of Material Treatment and Reuse versus Baseline
​
As stated above the approved strategy sentenced an estimated volume of 75,500m3 for off-site treatment before being returned to site for reuse (approximately 8 weeks later) and a further 60,000m3 with an undefined (but assumed off-site) treatment or disposal solution.
​
On the basis that the whole excavation volume of 135,000m3 was to be treated off site at a location say 25km distant it is estimated that the haulage activity alone would result in 14,444 vehicular movements exporting the soil for treatment, an equivalent number returning to site to be loaded (14,444) assuming 50% of the return loads carry a back-haul then a further c. 7,000 vehicle movements would be incurred, totalling 35,888no. 8-wheel tipper lorry movements each undertaking a c. 25km journey. The re-use of material resulted in 856,498 kgCO2e saved.
​
The works were conducted in accordance with the safe systems of work approved by Duo and BBV, including handling of potentially corrosive materials (chemox). Toolbox talks and frequent safety and compliance inspections were completed by all stakeholders.
​
​
​
​
​
​
​
​
​
​
​
​
​
​
​
“Jackson Remediation has identified effective
solutions to a range of contamination types
present across the site and allowed BBV to deliver
on the projects’ aspirations to maximise on-site
re-use in accordance with our MMP.”
Adrian Betts — Construction, Manager Earthworks, BBV
​
​
​


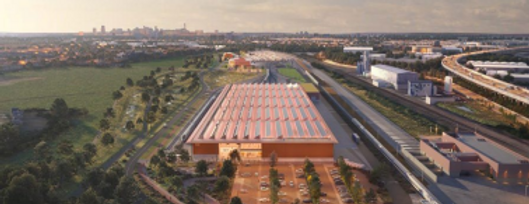
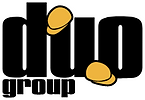

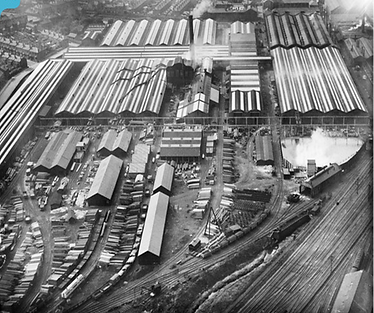
Phone:
​
+44 020 8145 5699
​
Email:
hello@jacksonremediation.co.uk
Address:
​
37–41 Mortimer Street

